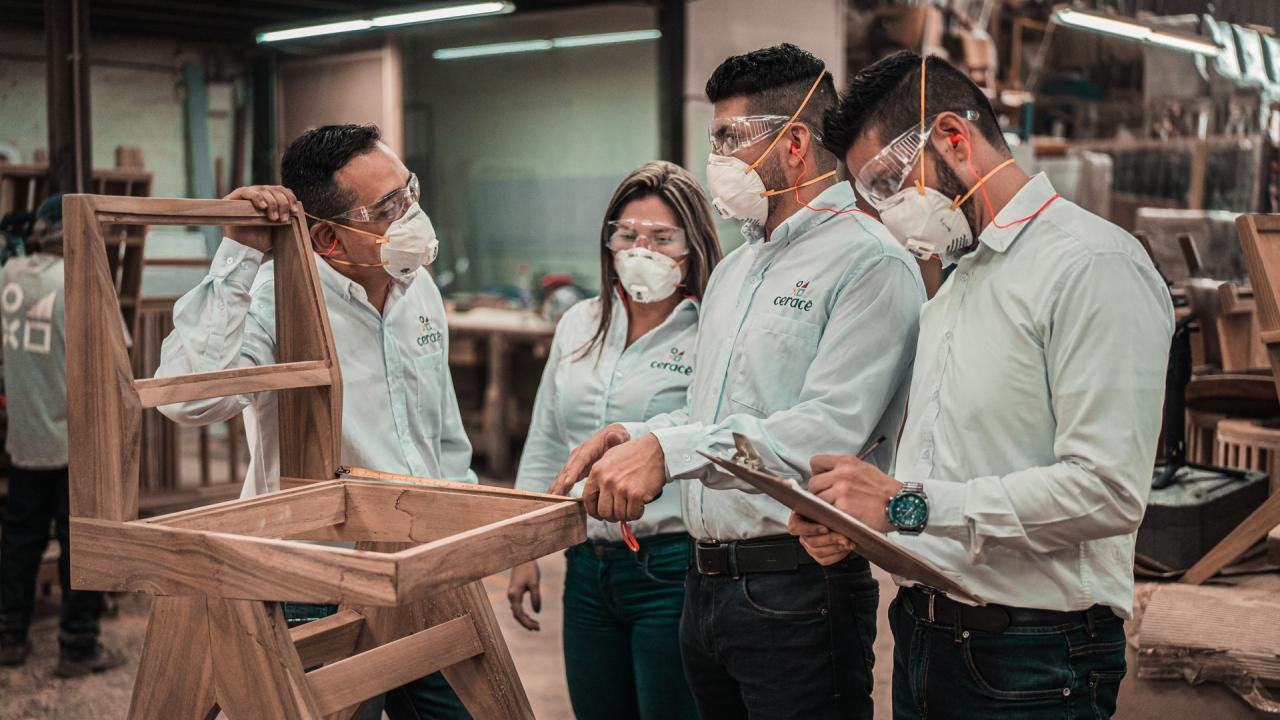
Underlying Causes of Workplace Injuries and Illnesses
Data from the Federal Bureau of Labor Statistics indicates that nearly 3.5 million workers are injured or fall sick on the job each year and over 5,147 are killed. In 2017, in California alone, over 466,600 fell sick and another 376 were killed, which was higher than the national average for that year.
When a worker suffers an injury or illness, it not only impacts the injured worker but also his or her family, co-workers, the employer, and society. Prevention programs are useful in helping to address these issues, with the goal of preventing injuries and illnesses and changing these statistics.
Many individuals might think that workplace injuries and illnesses happen because workers make mistakes and are careless. However, when employers look at an individual incident more closely, it becomes clear that multiple factors contribute to accidents in the workplace.
It is important to ask:
- Are there conditions in the workplace that caused this mistake?
- What is it about these conditions that allowed a mistake to occur?
- If procedures weren’t being followed, why weren’t they followed?
- Is there something wrong with the systems, policies, and/or conditions in the workplace that should be changed?
In WOSH Specialist trainings, we use the iceberg metaphor. The top of the iceberg represents the direct cause of the injury, the “what happened”. Other factors that contributed to the incident are represented by the part of the iceberg below the surface of the water or the underlying causes.
It is important to not only ask what happened, but also why it happened to help identify the hidden safety problems that played a role in the occurrence of the accident and might increase the likelihood of the accident occurring again in the future.
Often, there are a combination of underlying factors involved in an incident. When looking for underlying causes, you may find problems in one or more of these areas:
- Job tasks and procedures: look at the way they are designed to ensure they are safe and practical
- Work environment: poor work area set up, poor air quality, high/low temperature, etc.
- Management and organization: inadequate safety program, lack of resources, poor communication, no system for reporting problems, or no involvement by management
- Individual worker or workforce: inexperience, inadequate training, fatigue, stress, or problems with communication
When analyzing a task to identify the hidden hazards, it is important to ask questions such as:
- Are work processes and equipment designed properly?
- Are operating procedures adequate and clear?
- Are work rules realistic?
- Is training adequate?
Everyone makes mistakes, but when mistakes happen, it is important to ask why. The best way to prevent injuries is by fixing the underlying policies, procedures, and conditions that contribute to them.
Additional Resources
- Learn more about our free Worker Occupational Safety and Health (WOSH) Specialist trainings
- Look out for next month’s Próximamente, as it will cover What Are Job Hazards? (WOSHTEP Program, Labor Code Section 6354.7)
This article is based on the Worker Occupational Safety and Health Training and Education Program (WOSHTEP) administered by the Commission on Health and Safety and Workers' Compensation in the California Department of Industrial Relations through interagency agreements with the Labor Occupational Health Program at the University of California, Berkeley; the Western Center for Agricultural Health and Safety at the University of California, Davis; and the Labor Occupational Safety and Health Program at the University of California, Los Angeles.